Super-ceramiche per produrre energia sostenibile (ma anche orologi e veicoli spaziali...)
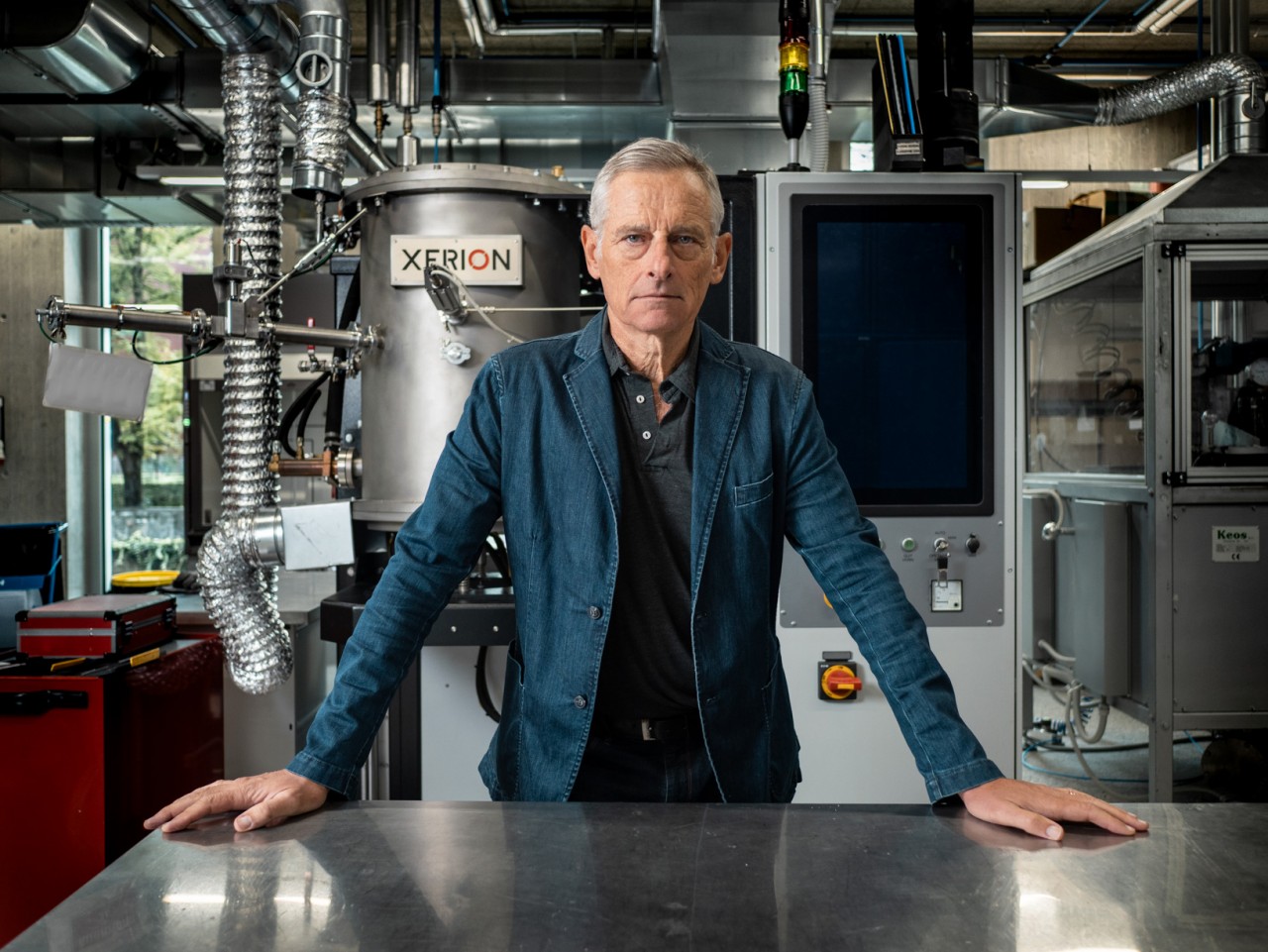
Intervista ad Alberto Ortona, responsabile del Laboratorio di materiali ibridi della SUPSI, uno dei più avanzati in Svizzera. Queste ceramiche speciali hanno prestazioni d’eccezione e altissima resistenza di Monica Nardone
Dalla preistoria all’hi-tech: la ceramica, nata con l’argilla per costruire vasellame, negli ultimi decenni si è evoluta diventando una "super ceramica", ovvero un materiale avanzato cruciale per tutte quelle applicazioni tecnologiche che richiedono resistenza ad alte temperature e ad ambienti altamente corrosivi, ed elevata trasparenza, con applicazioni che vanno dal campo automobilistico, aerospaziale, aeronautico, fino all’orologeria e all’energia. In questo ambito, nel Canton Ticino vi è un laboratorio di livello europeo, unico in Svizzera. È il Laboratorio di materiali ibridi della Scuola universitaria professionale della Svizzera italiana (SUPSI), attivo presso il Dipartimento tecnologie innovative. Dedicato alla ricerca applicata e alla formazione nel campo della scienza e tecnologia dei materiali, il Laboratorio è specializzato nello studio di materiali ceramici porosi, progettati con metodi avanzati, simulati mediante l’utilizzo di calcolatori numerici, realizzati con la stampa 3D e infine sperimentati, per testarne le proprietà meccaniche e termiche.
Questi materiali non sono basati sull’argilla come le ceramiche tradizionali, ma su composti formati principalmente da ossidi, carburi e nitruri, come ossido di magnesio, carburo di silicio, nitruro di silicio. Condividono con le ceramiche tradizionali il processo di "cottura": in pratica, dopo che i materiali vengono prodotti devono essere cotti, cioè sottoposti a trattamenti termici fino a 2.200 gradi per diventare super-ceramiche. A differenza delle ceramiche tradizionali, inoltre, hanno una struttura porosa come le spugne, e il segreto della loro efficienza e delle loro caratteristiche è dovuto al fatto che la forma della porosità e il modo in cui è disposta sono progettate in laboratorio. «Siamo all’avanguardia nel settore - spiega il professor Alberto Ortona, responsabile del Laboratorio - perché abbiamo trasformato i materiali porosi, per esempio le spugne con una porosità a caso, in materiali la cui porosità è controllata, ossia configurata nelle forme desiderate». In pratica, aggiunge Ortina, «siamo in grado di progettare e realizzare delle schiume con forme che noi disegniamo al calcolatore». In questi materiali sia la forma della porosità, che il modo in cui è disposta, cioè la topologia, sono la chiave per conferire al materiale le caratteristiche volute.
Questo elemento, continua Ortona, è cruciale perché «alcune applicazioni ingegneristiche ormai sono estremamente "spinte" da un punto di vista delle prestazioni, e per costruire una macchina che abbia alte prestazioni occorrono materiali molto avanzati». Molte sono le aziende, svizzere e non solo, interessate a realizzare nuovi prodotti con questo tipo di materiali, per avere un vantaggio strategico sul mercato. Non per niente il Laboratorio della SUPSI conduce il 90% dei progetti di ricerca in collaborazione con aziende e con altri centri di ricerca come EMPA (Laboratori federali svizzeri per la scienza e la tecnologia dei materiali), e il Politecnico federale di Losanna (EPFL).
Molte sono le possibili applicazioni di queste super ceramiche, ma in questo momento il settore più promettente è quello dell’energia: «Questo settore - dice Ortona - è centrale a livello europeo, perché l’industria sta cercando nuovi modi per produrre, immagazzinare e trasferire energia. In questo ambito, per esempio, stiamo lavorando nel campo del solare termico concentrato, che utilizza specchi per concentrare, appunto, la luce solare su una torre. Il calore di centinaia di specchi focalizzato in un punto molto piccolo sviluppa temperature altissime che possono essere sopportate solo da materiali ceramici, perché altri materiali si fonderebbero». Ultimamente, precisa Ortona, «si lavora tantissimo anche alla produzione di idrogeno attraverso la decomposizione di sostanze come acqua o idrocarburi. La decomposizione di queste sostanze avviene attraverso il calore, e le super ceramiche entrano in campo nelle apparecchiature che devono resistere a questo trattamento». In tale ambito, il Laboratorio di materiali ibridi, insieme al gruppo attivo presso l’Istituto di ingegneria meccanica e tecnologia dei materiali della SUPSI, coordinato dal professor Maurizio Barbato, sta portando avanti un progetto europeo chiamato Hydrosol, che mira a produrre idrogeno a partire da acqua e CO2.
Proprio per la straordinaria resistenza al calore, queste ceramiche sono state impiegate anche nel progetto europeo ECCO, svolto con il gruppo tedesco dell’acciaio ThyssenKrupp. Nelle linee per la produzione di acciaio, per evitare che le apparecchiature arrugginiscano, si spruzza una vernice diluita con un solvente che poi evapora, e il vapore è convogliato in una torre dove viene bruciato, producendo CO2, cioè anidride carbonica. «L’idea del progetto - spiega Ortona – è quella di ridurre la produzione di CO2, facendo diventare i solventi che evaporano il combustibile per la linea di produzione, in modo da chiudere il ciclo. Tutto questo ha richiesto lo sviluppo di una macchina basata su ceramiche porose, attraverso le quali viene fatto passare il solvente mentre viene bruciato».
La resistenza al calore ha portato questi materiali anche nello spazio: il laboratorio della SUPSI ha collaborato recentemente anche con l’Agenzia Spaziale Europea (ESA) per realizzare delle viti in ceramica resistenti al calore, destinate a veicoli spaziali che, viaggiando a velocità ipersoniche, si riscaldano enormemente. Molte le applicazioni anche nel settore automobilistico: con EMPA il laboratorio della SUPSI, per esempio, ha realizzato dei filtri catalitici, testati con successo per Audi.
Questi materiali trovano applicazione anche nell’edilizia, in particolare per rendere le abitazioni autonome dal punto di vista termico senza l’utilizzo di combustibili fossili e di corrente elettrica per il riscaldamento. In merito a questa applicazione, il laboratorio ticinese ha appena iniziato un progetto europeo per l’immagazzinamento termochimico del calore. In pratica, spiega Ortona, «trasformiamo il calore d’estate in energia chimica, e d’inverno ritrasformiamo l’energia chimica in energia termica. Noi ci occupiamo di produrre materiali ceramici per massimizzare questa trasformazione».
Le super ceramiche sono anche straordinariamente dure e trasparenti, trovando applicazione in un settore che non ci si aspetta, come quello dell’orologeria. «In un orologio di qualità svizzero – dice Ortona - una buona percentuale del materiale è fatto di ceramica avanzata, per questioni estetiche e di precisione, perché se i materiali sono molto duri possono essere lavorati con molta precisione».
LA PROGETTAZIONE - Per arrivare a questi materiali con prestazioni così elevate, determinante è il metodo di progettazione, per il quale si distingue il laboratorio della SUPSI, che è basato su simulazioni con calcolatori, la realizzazione con la stampa 3D e la caratterizzazione che ne verifica le proprietà meccaniche e termiche. «Siamo in grado di progettare e realizzare materiali ceramici porosi le cui forme sono disegnate al calcolatore - spiega Ortona. - Attraverso codici numerici generiamo delle forme che poi inviamo alla stampante 3D. Questa macchina a sua volta stampa l’oggetto, che poi viene convertito in ceramica attraverso trattamenti termici fino a 2.200 gradi».
Insomma, è un po’ come fare un vaso: prima si realizza la forma a freddo e poi lo si cuoce, trasformandolo in ceramica. «In collaborazione con il professor Barbato - dice Ortona - facciamo anche una serie di simulazioni al computer di questi oggetti ancor prima di utilizzarli. Dunque, quando realizziamo un componente siamo sufficientemente sicuri di come si comporterà». L’ultima fase è la caratterizzazione, ossia la fase di test per provare le proprietà meccaniche e termiche dei materiali, e per verificarne la microstruttura con un microscopio a scansione elettronica.
COSTI ANCORA MOLTO ALTI - Il problema di questi materiali, che li rende ancora poco scalabili per le aziende, rimane quello dei costi, tuttora molto elevati. La SUPSI si sta impegnando per rendere questi processi economicamente sostenibili. «Finora – conclude Ortona - ci siamo concentrati sulle prestazioni e non su questi aspetti, ma questa è la sfida del futuro».