Alla Biennale di Venezia gli "scarti"
dei marmi di Arzo riciclati
da un’innovativa stampante 3D
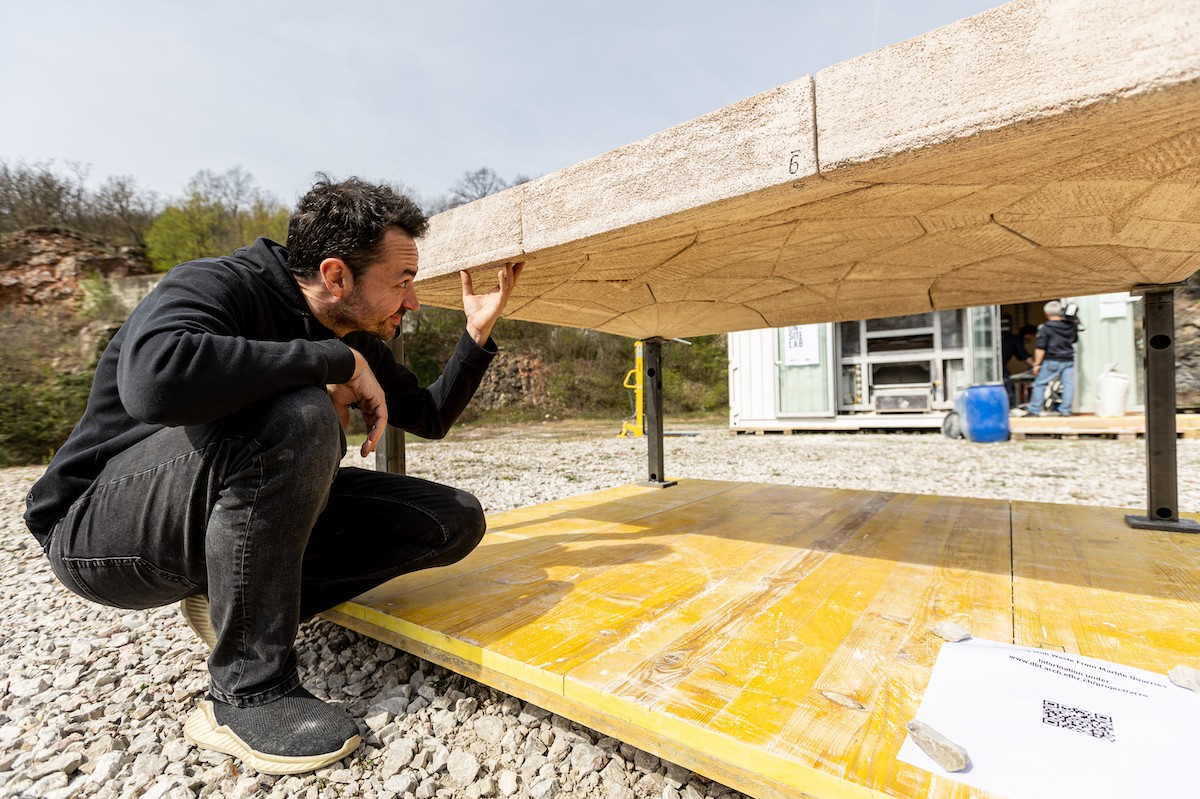
Collaborazione SUPSI-Politecnico di Zurigo. Si cercano soluzioni per contribuire al recupero dell’enorme quantità di residui edili che si accumulano ogni anno: ben 57 milioni di tonnellate in Svizzeradi Paolo Rossi Castelli
Da una parte i residui delle ex-cave di marmo di Arzo, dall’altra il metacaolino, un materiale che permette di creare un “amalgama” molto resistente e, per certi aspetti, più ecologico del classico calcestruzzo: questo mix può essere poi lavorato per ottenere vari tipi di manufatti, grazie a una stampante 3D sperimentale, che l’11 aprile è stata presentata fra le alte pareti delle cave dagli ingegneri della SUPSI (Istituto Scienze della Terra) e del Politecnico federale di Zurigo. «Vogliamo proporre, con questa stampante, una possibile soluzione per contribuire al recupero, almeno in parte, dell’enorme quantità dei materiali di scavo (non solo di quelli di Arzo), che altrimenti vengono smaltiti nelle discariche, con costi molto elevati - ha spiegato Filippo Schenker, ricercatore SUPSI. - Si stima che ogni anno in Svizzera i residui edili raggiungano i 57 milioni di tonnellate. E il problema è molto presente anche in Ticino».
Foto di Chiara Micci / Garbani Guarda la gallery (11 foto)
La stampante è stata costruita, letteralmente, da Pietro Odaglia, ricercatore dell’équipe di Benjamin Dillenburger (cattedra di Digital Building Technologies al Politecnico di Zurigo). Questa apparecchiatura utilizza ugelli speciali, realizzati per l’occasione, che consentono di ottenere una raffinata precisione di esecuzione. Ma come funziona questa “macchina”? Semplificando molto, possiamo dire che filtra i residui dell’estrazione del marmo, selezionando quelli delle giuste dimensioni (piccole). Poi questi frammenti vengono sminuzzati e mescolati al metacaolino, ottenendo una miscela che la stampante distribuisce lungo un disegno predefinito dai ricercatori, procedendo strato dopo strato. Il risultato finale è un elemento costruttivo con un’impalcatura ad arco, molto resistente, che potrà essere utilizzato come elemento di rivestimento delle facciate degli edifici, ma anche per costruire la “soletta” di una stanza. Attualmente è stato realizzato un primo prototipo, che verrà esposto alla Biennale Architettura di Venezia, in programma dal 20 maggio al 26 novembre. Per "produrlo" la stampante ha dovuto lavorare circa 12 ore, a cui sono seguite altre 12 ore di “riposo” del manufatto.
Guardando il prototipo che verrà portato a Venezia, colpisce la presenza di numerosi “vuoti” sulla sua superficie, che non appare come un blocco “monolitico”, ma quasi come una scultura ornamentale (un bassorilievo). «In effetti si risparmia il 70% per cento di materiale, con questa tecnica, rispetto ai sistemi tradizionali - conferma Francesco Ranaudo, ricercatore dell’Institute of Technology in Architecture dell’ETH. - La stampante deposita con estrema precisione la miscela, destinata a indurirsi subito dopo, solo lungo le linee di forza (tracciate da software sofisticati), che servono per dare la massima resistenza al manufatto».
Com’è nata la collaborazione fra la SUPSI e il Politecnico di Zurigo? «Quasi per caso, nel 2019 - racconta Filippo Schenker. - Ho incontrato Vera Voney (cattedra di Sustainable Construction all’ETH, ndr) in un corridoio di Zurigo. Stava lavorando con Pietro Odaglia a una stampante 3D a basso impatto ambientale. Dal canto nostro, alla SUPSI eravamo impegnati in un progetto per recuperare gli scarti di cava. Perché non farlo insieme? E così è avvenuto, grazie anche a un finanziamento di Innosuisse (progetto REBJP - Binder Jetting for direct application of recycled materials)».